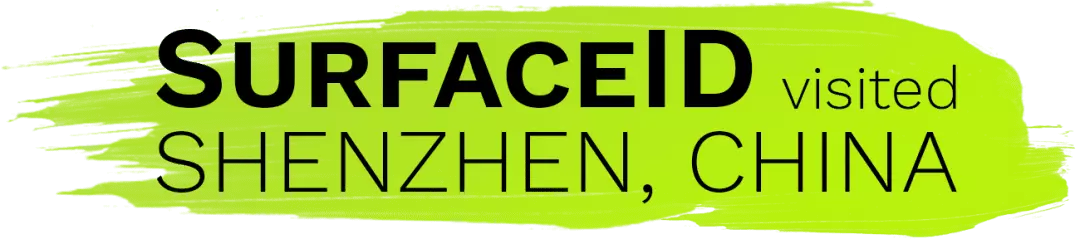
One of our contracts, the Knight Trainer Pro (KTP), had us visit many factories around the city. The mission was to inspect all of the production parts for the KTP mass production order, build one complete and working badminton training machine on location using those same production parts, then ship all of the remaining parts back to our office in Montreal.
1. Arrival
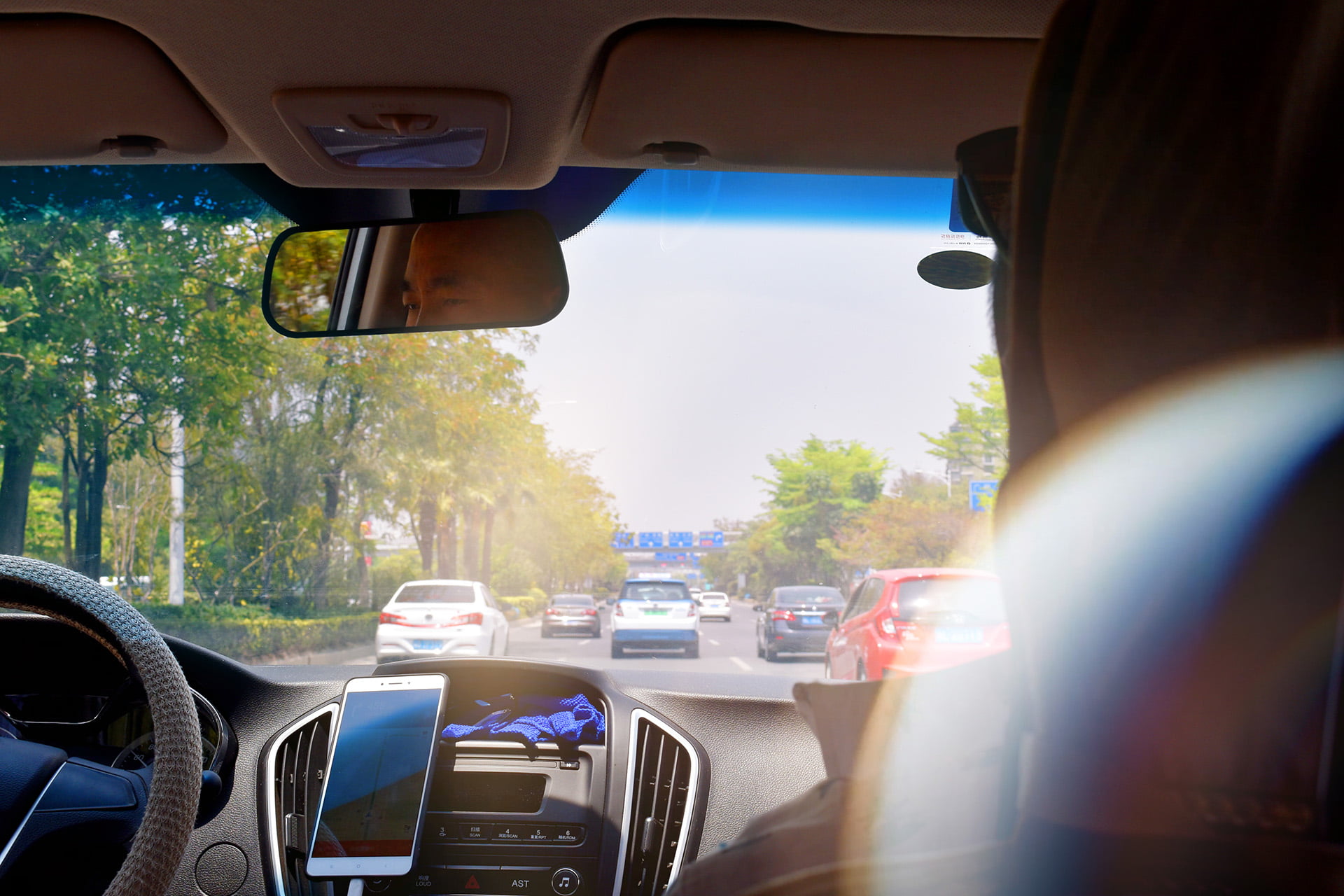
After almost an entire day spent in flights and airports, our plane finally landed in the middle of a hot April night. Trying not to get scammed by overpriced, unlicensed taxis, we waited one more hour in line at Shenzhen’s airport for the regular taxis. Then we went straight to our hotel for a few hours of sleep.
At 9am, our Chinese engineer organized a ride on Didi—their Uber equivalent—to get us to work.
Every Internet app seems to have a local equivalent. Most Google services and many western websites don’t work in China. For example, they use WeChat, and China blocks most messaging apps like Facebook / Messenger / WhatsApp, Twitter, Telegram, KakaoTalk (most popular in South Korea), Line (most popular in Japan), etc. Popular community boards are also blocked often.
WeChat has so many features, especially when it comes to businesses and transactions, that it became crucial in this country. With a billion users and a state-sponsored initiative of “smart living”, it processes the everyday lives of many.
It is important to come advised and prepared, as to not start the trip in frustration.
Close to our hotel was the metal factory, where the manager let us use most of his assembly space for 12 days straight. They also make their own products, like fidget spinners. The CEO and his staff were very helpful but our Chinese engineer was also essential to make our manufacturing requests understandable.
A lot of factories like this one have an apartment wing that the employees can benefit from if they need housing next to the workplace. All neighbors are coworkers and opening the windows will remind you where you are, but in terms of proximity and affordability, it beats anything else.
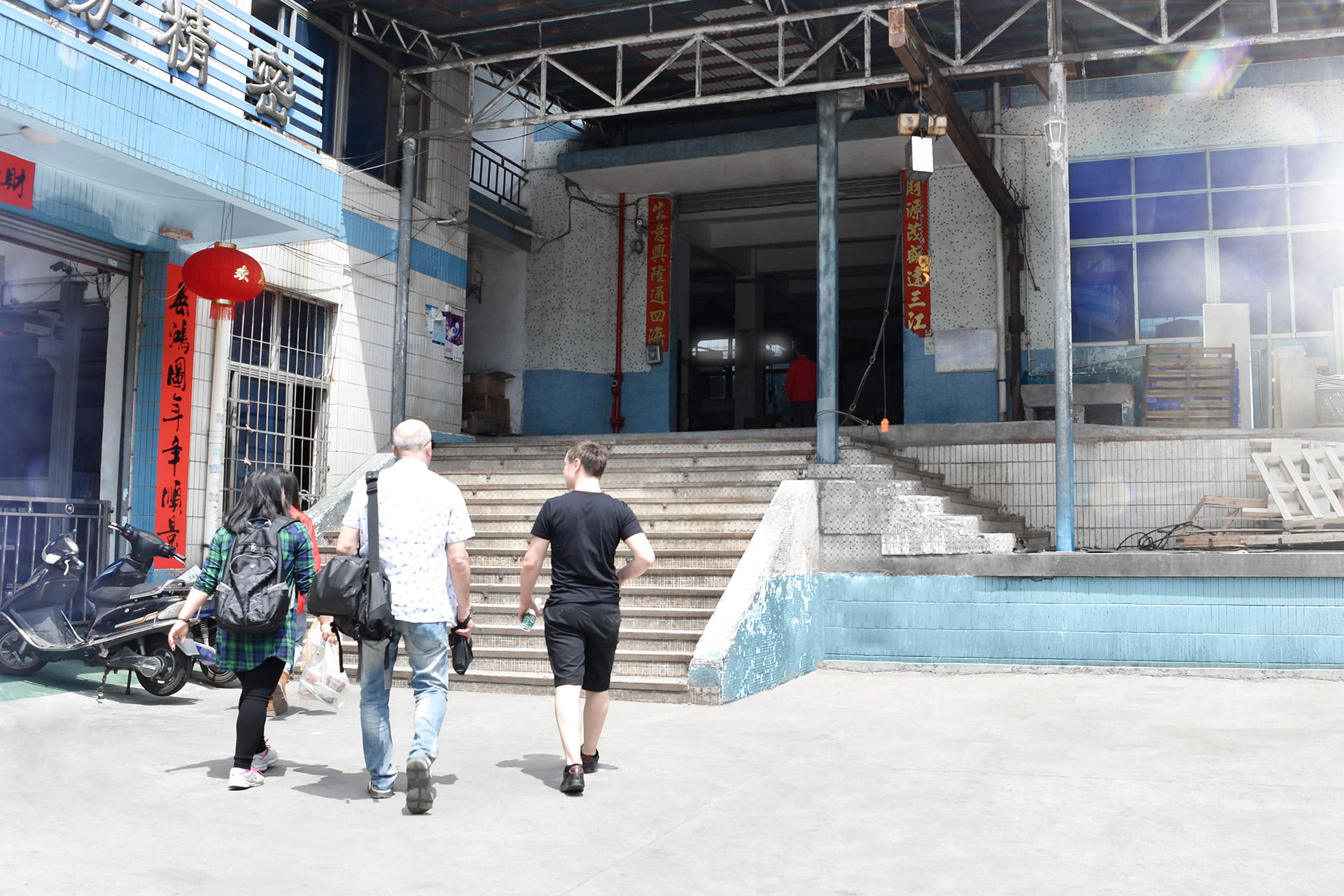

2. Making an inventory
Each box had to be opened. Each part had to be inspected. And everything had to be repackaged to take as little space as possible and to travel more safely across the ocean.
Our engineer removed one of each part to start assembling the first production KTP and make sure that all parts fit correctly.
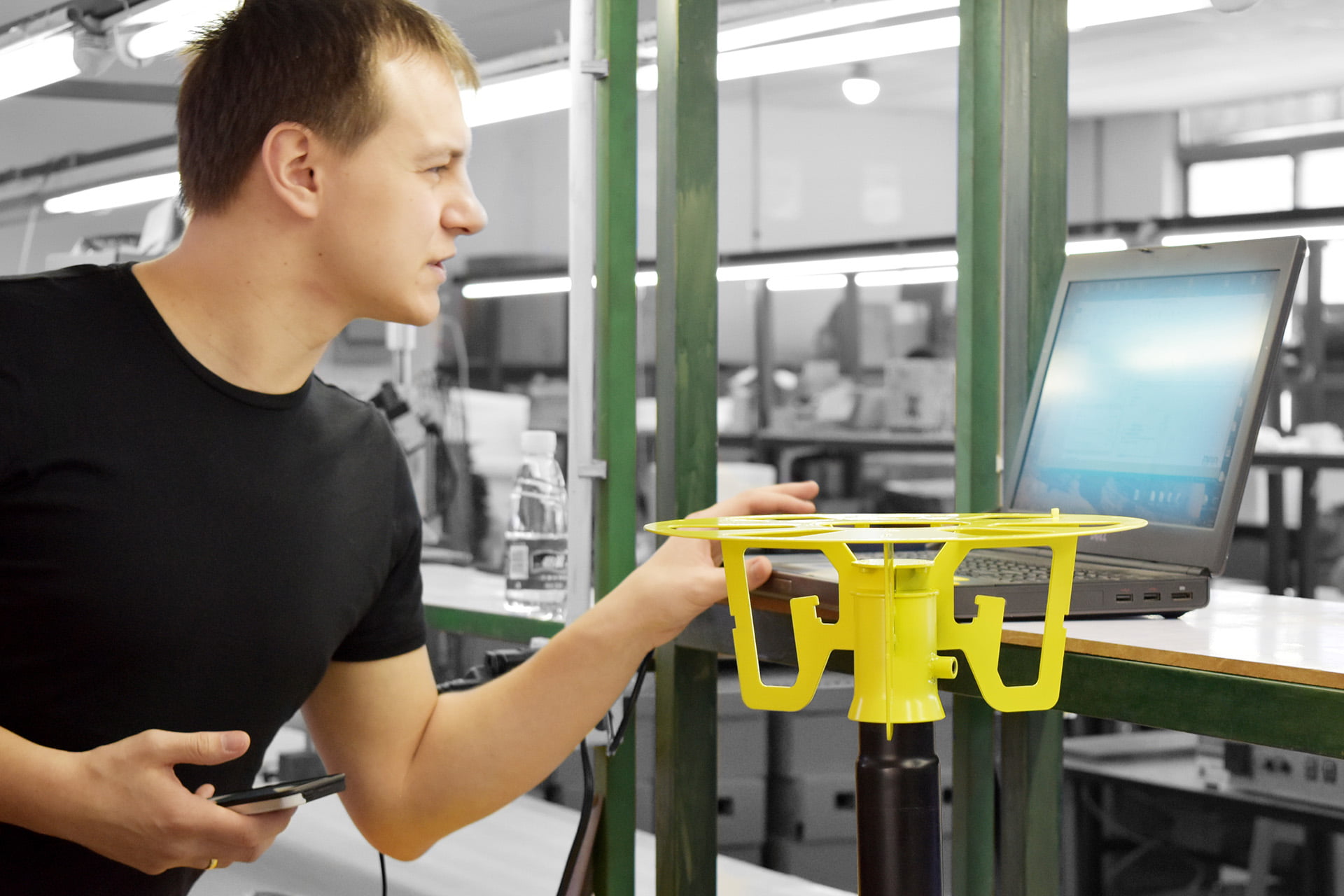
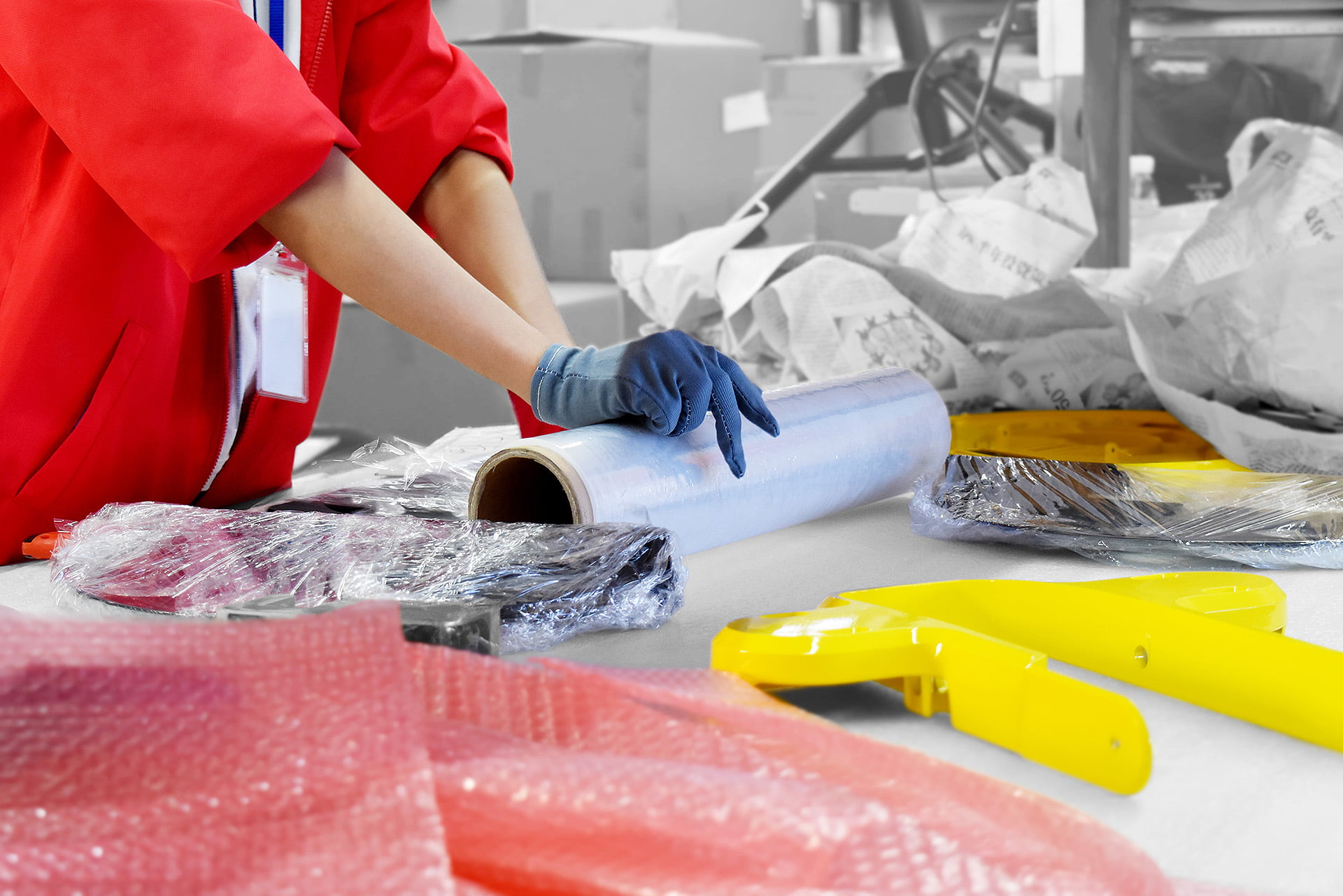
When parts were done being inspected and inventoried, we would use plastic and bubble wrap and put them in international boxes to ship to Canada. The newspapers that were first used as a wrapping by different factories were not a good enough protection for our parts and couldn’t be shipped outside the country for legal reason.
3. Little big adventure
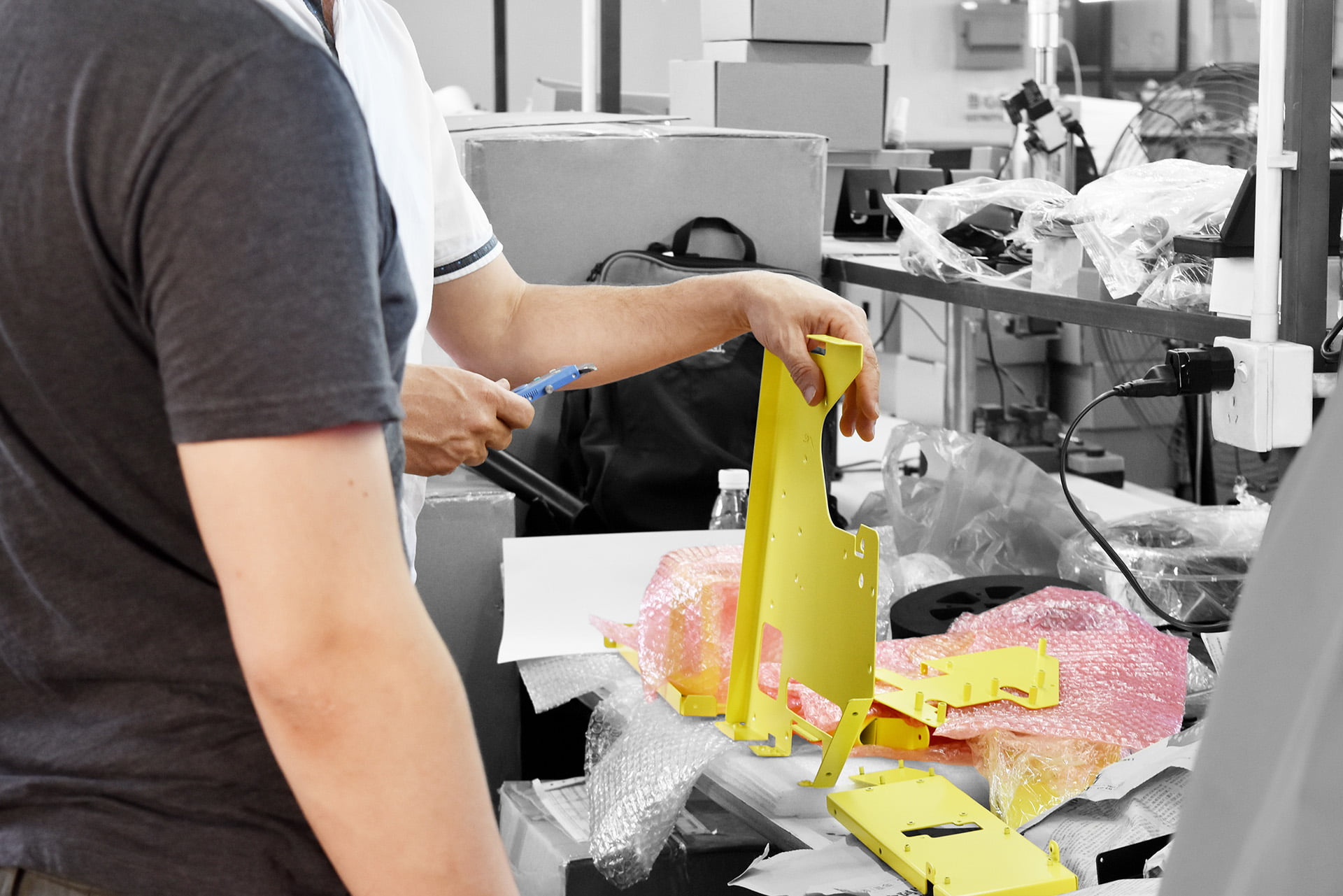
Assembling a machine in China with production pieces (as opposed to prototype pieces) was important.
As we were unboxing and assembling, we noticed that some of our sheet metal parts were not painted correctly. The screwholes had been painted in the inside, clogging up the threads and the screws would not go in, which of course prevented building the KTP.
Because the order was in progress, we decided to tap the few ones in our possession ourselves. For the rest, we had to call the painting factory and tell them to stop what they were doing immediately.
Because of our limited timeframe in China, we didn’t want to risk making only that phone call. Fortunately, other manufacturing facilities were also enclined to let us visit and inspect the work done. With assistance, we explained how the painting should have been done. The workers went back to it immediately—with silicone plugged screwholes this time.
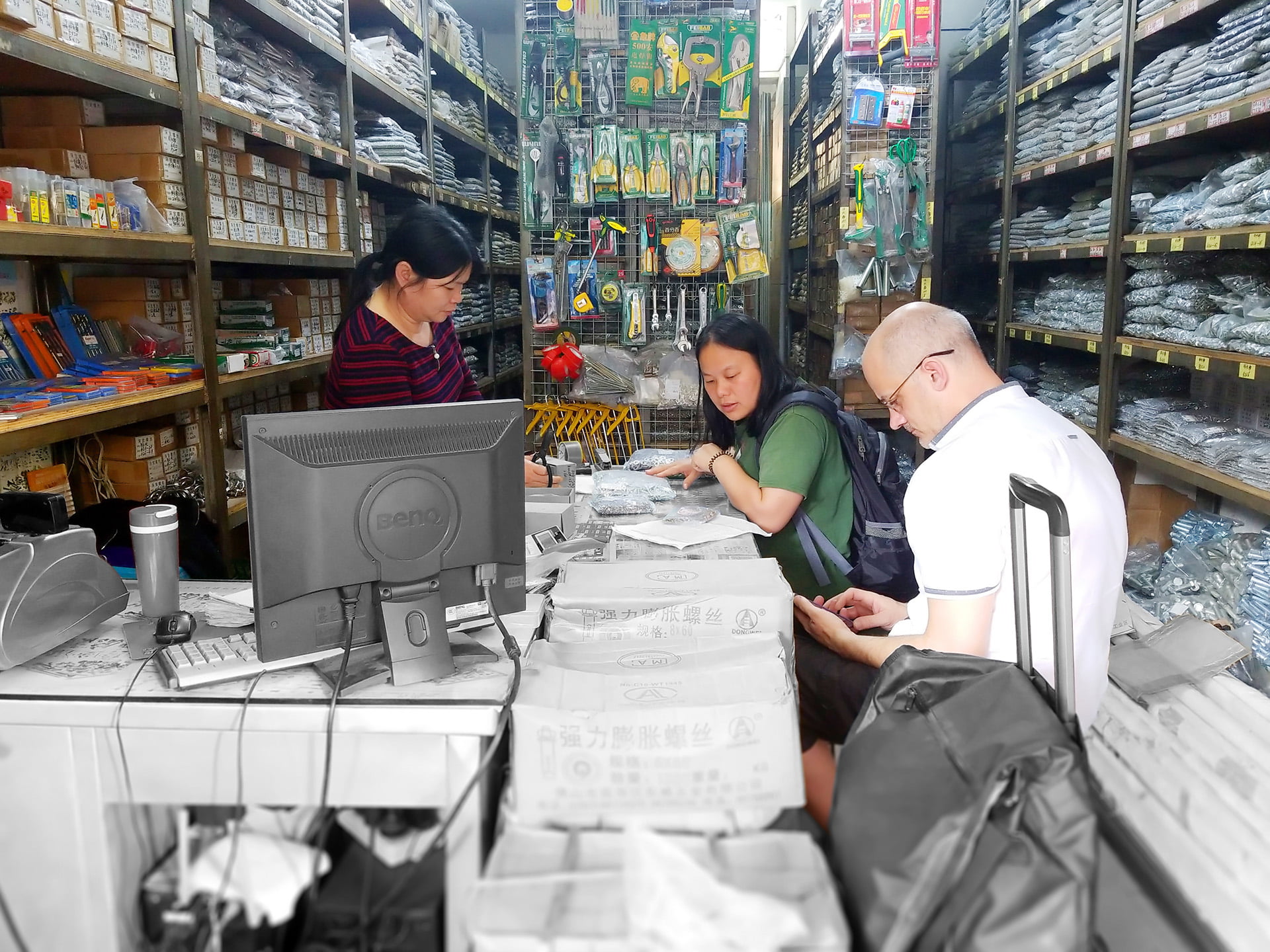
Shenzhen has many neighborhoods that focus on selling one specific type of tools or material for manufacturing. So if you’re looking for wood or porcelain or screws, you can focus all of your efforts in one location, for many shops there would cater to your needs.
This photograph shows the interior of a screw shop where we found USA standard sized screws instead of metric ones.
We held a fight between the factory manager and a dangerously close, working KTP. The other video shows a part of the winner’s body armor being cut through CNC machining.
4. Meetings and networking
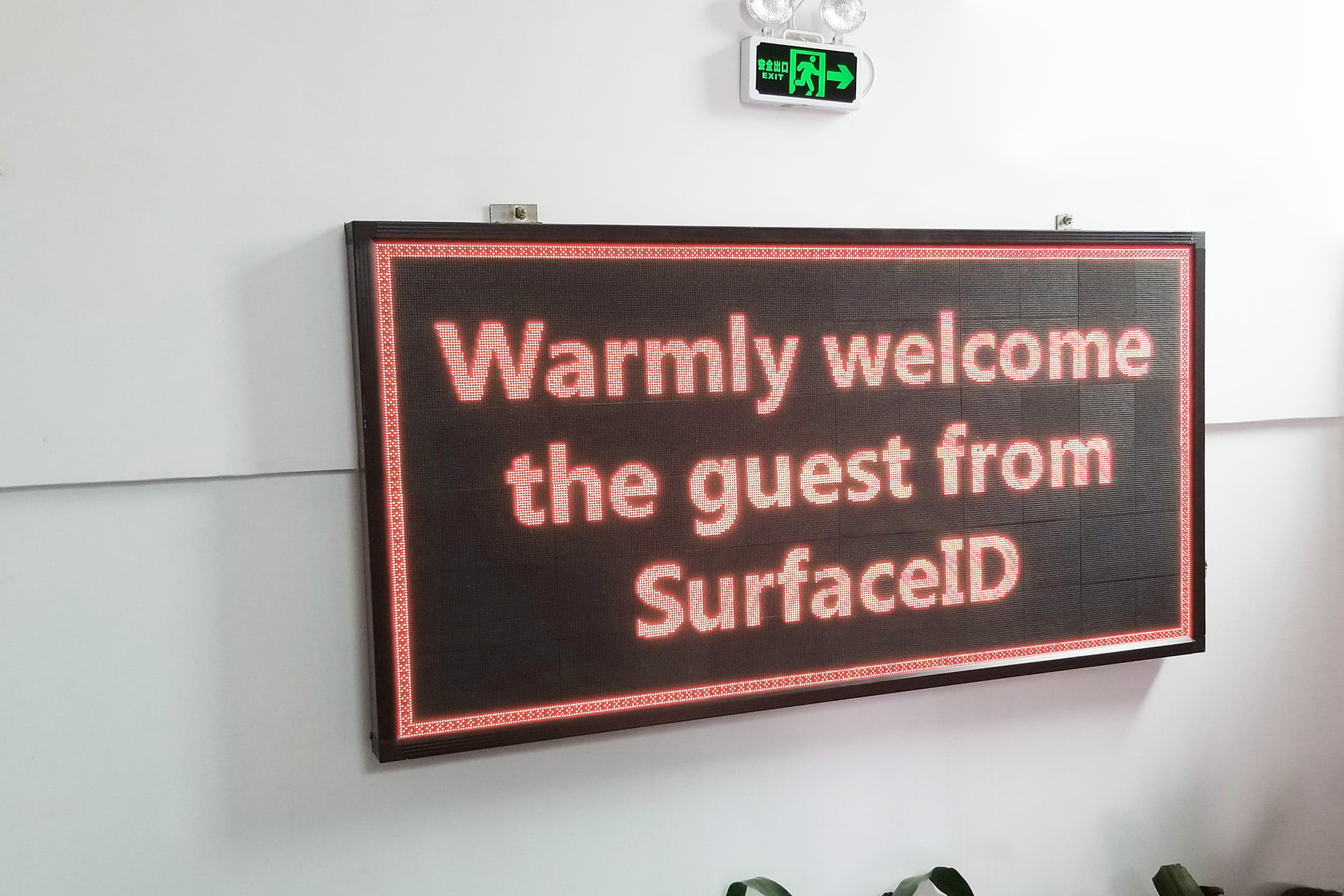
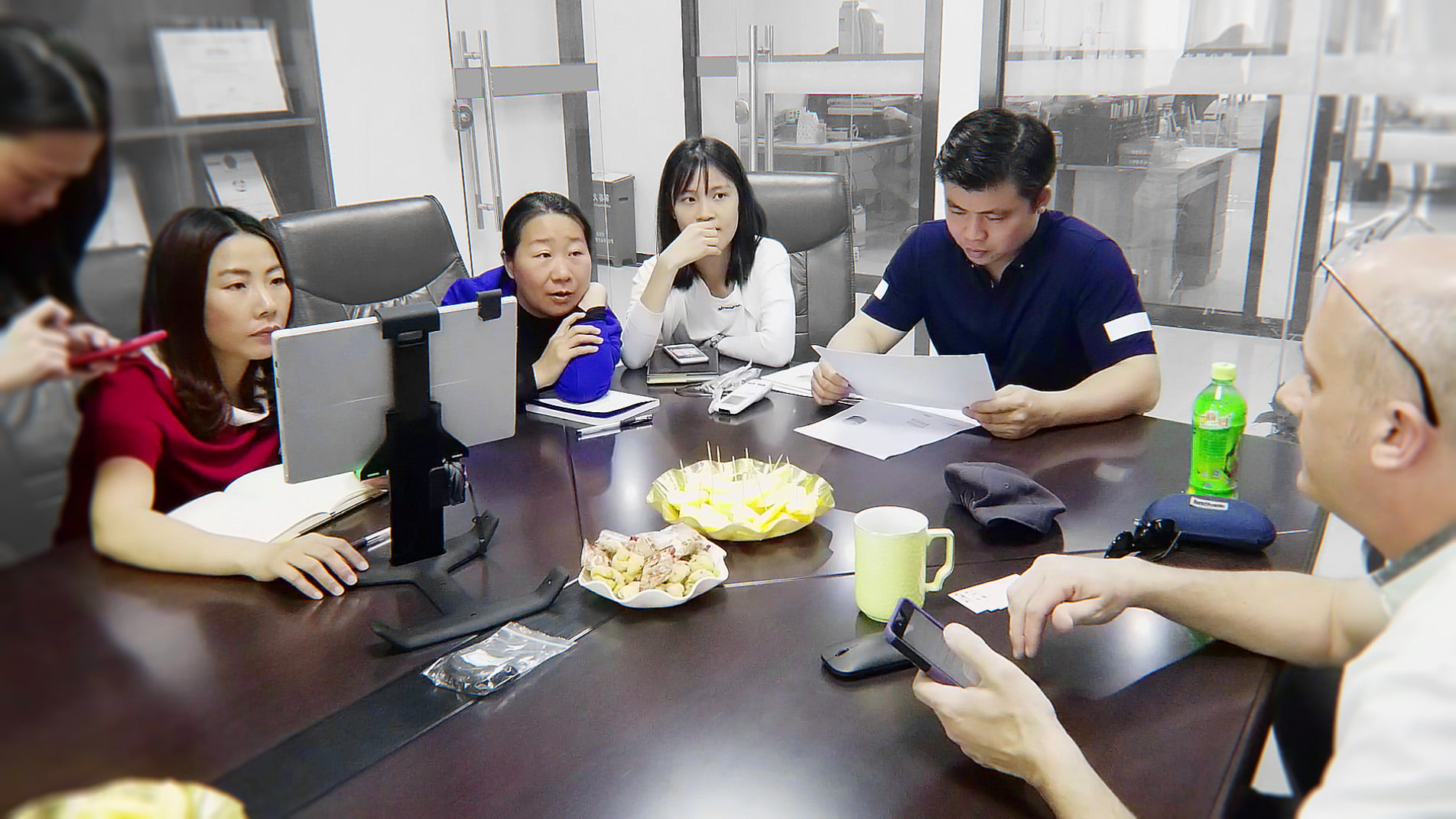
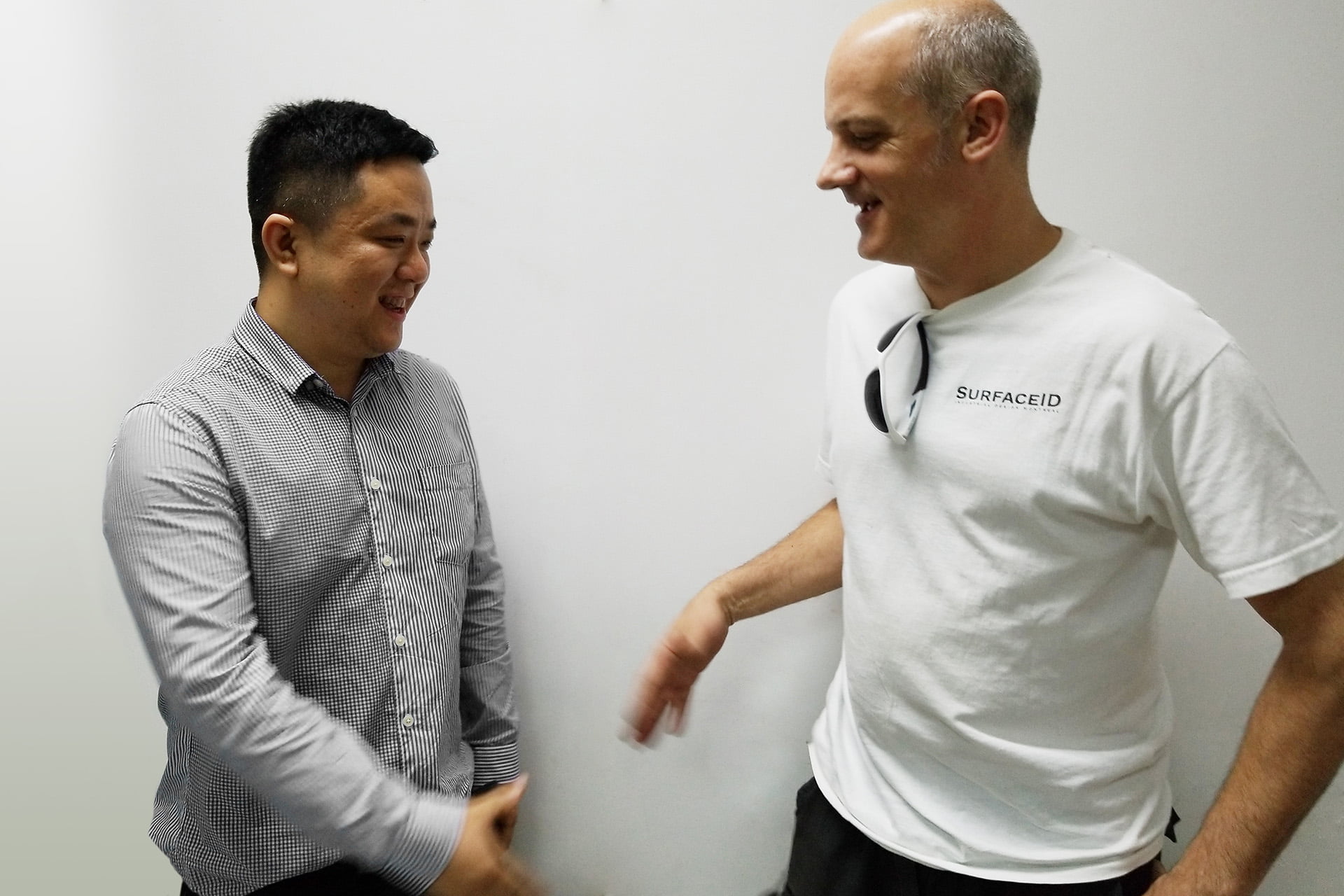
5. Shipping to Canada and assembly line
A truck came to pick up our dozen of palettes which would then ship by boat. Shipping by airplane would have been faster but at a greater cost and with more restrictions (palette size, sorting of goods, etc).
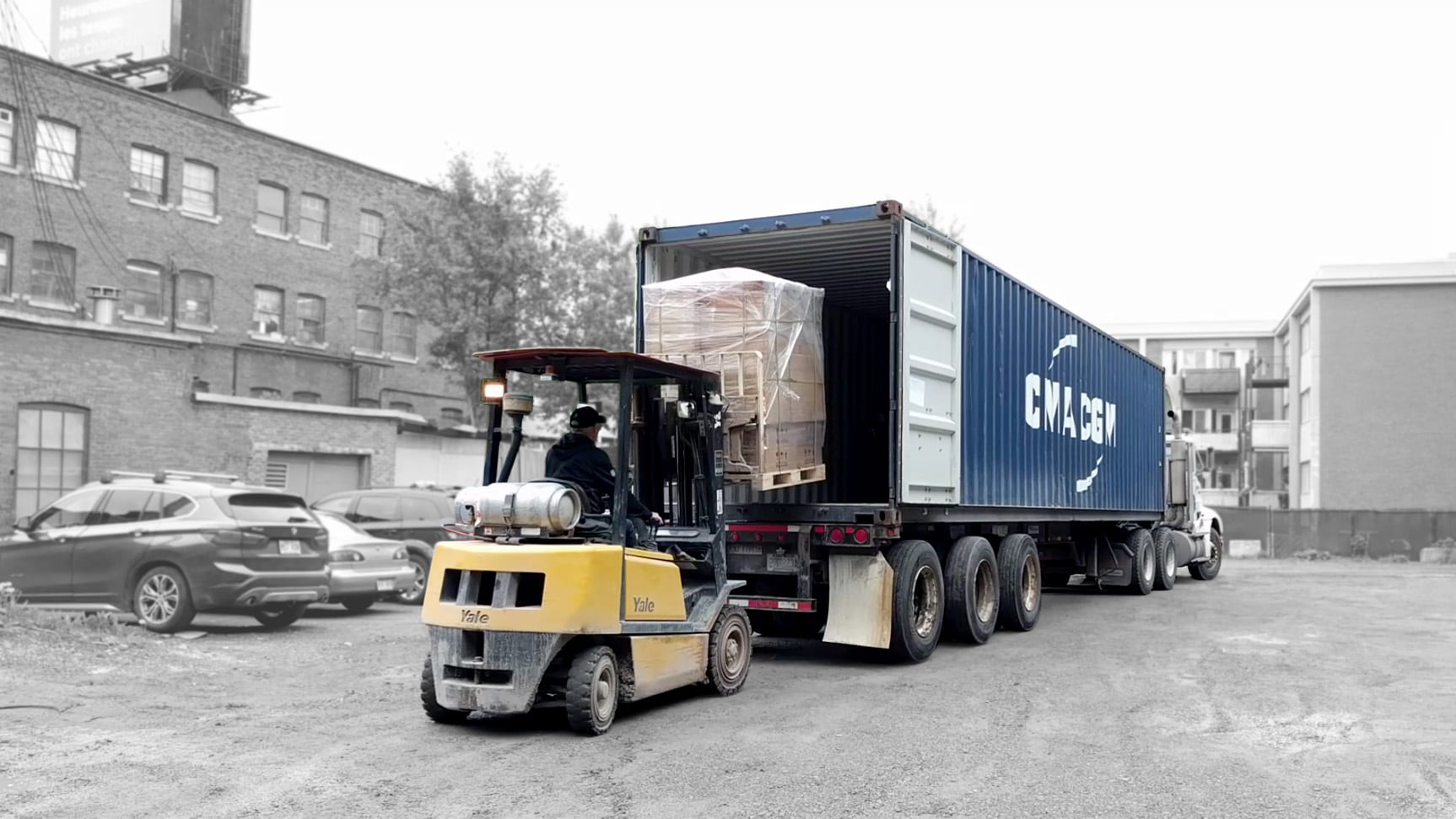
A few weeks and 12,500 km later, we received all palettes in our office in Montreal. Manufacturing success!
Our office is not factory-sized, and we play room-Tetris with the dozen of the palettes. With great nostalgia, we started unpacking everything again. Trapped between two boxes, we even found a pair of sunglasses that we thought lost in China!
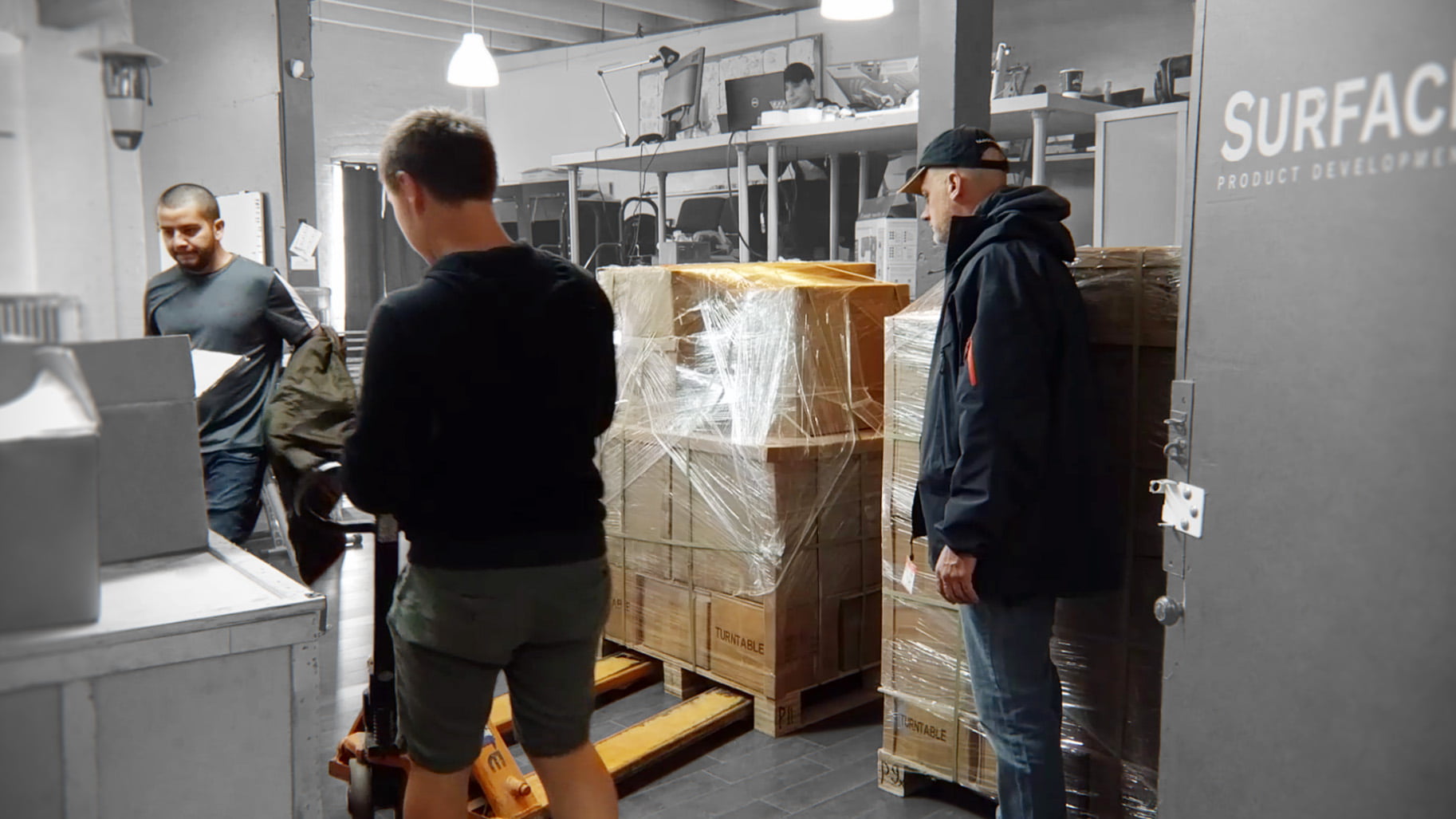
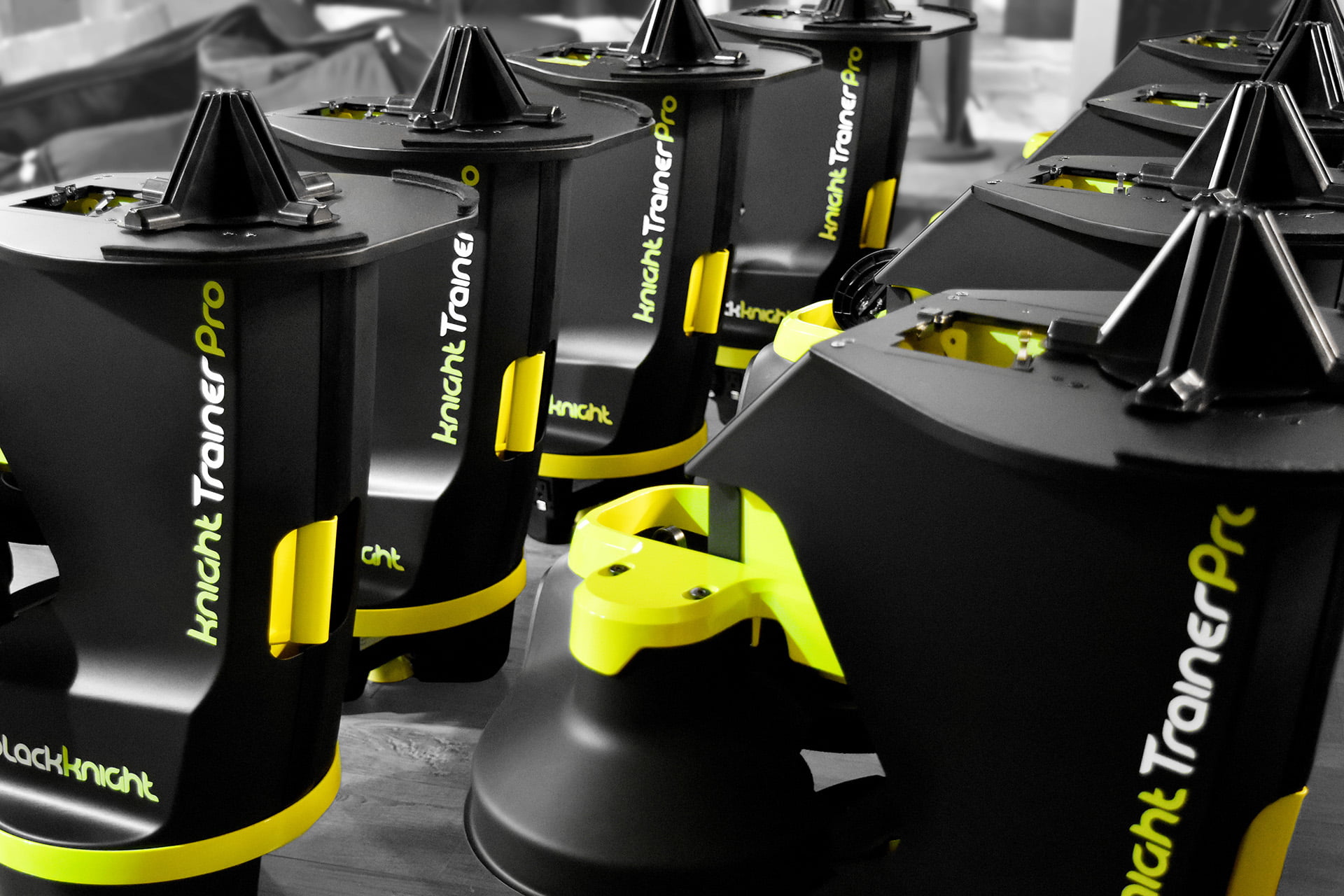
With all the hardware in our hands, we could start our own assembly line for manufacturing and fulfill the very first order of Knight Trainer Pro.