Well, the most correct but annoying answer is: it depends! There is no fixed price for hiring an industrial design firm. It mostly depends on the scope of the project.

Venous Light Medical Design Sketch Rendering
What are we defining?
Industrial design is a profession that focuses on the form, function, and—of course—the user experience of a product. It is a creative job, but, more often than not, the products will be mass manufactured. This means that it is also the designer’s job to design around manufacturing constraints.
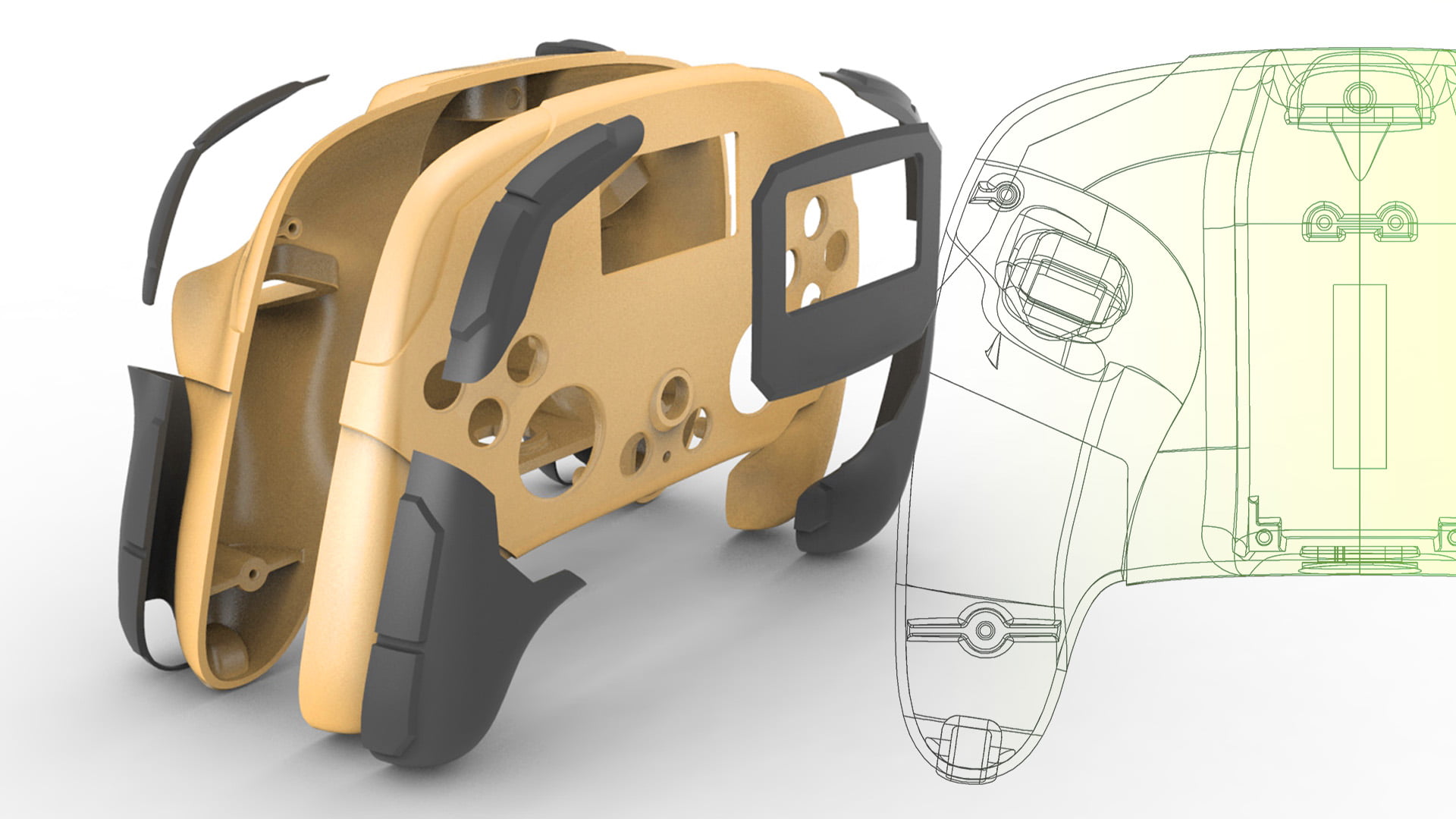
The cost of industrial design we discuss in this article is not to be confused with the price of an object. The price of an object is determined by many factors. This includes materials, the location of manufacture, the part count, assembly, the shipping and delivery costs, etc. This information is certainly important during the production of an object. However, the cost of the industrial design itself is separate from the price of a single object. .
In this post, we will be discussing the cost of design development, before manufacture and production begins.
How do we quantify the cost?
Quotes are estimated mainly by the time spent on a project. An established industrial design firm will know based off of experience how much work will be required to complete a project. However, the number of hours spent on a single project can vary greatly based on the scope of the project. Different services also have different fees. For example, a “one-part wonder”, such as a new design for a silicone trivet will have a short lead time. Whereas a product such as an LCD screen with many electronic parts will have wildly different scopes and budget.
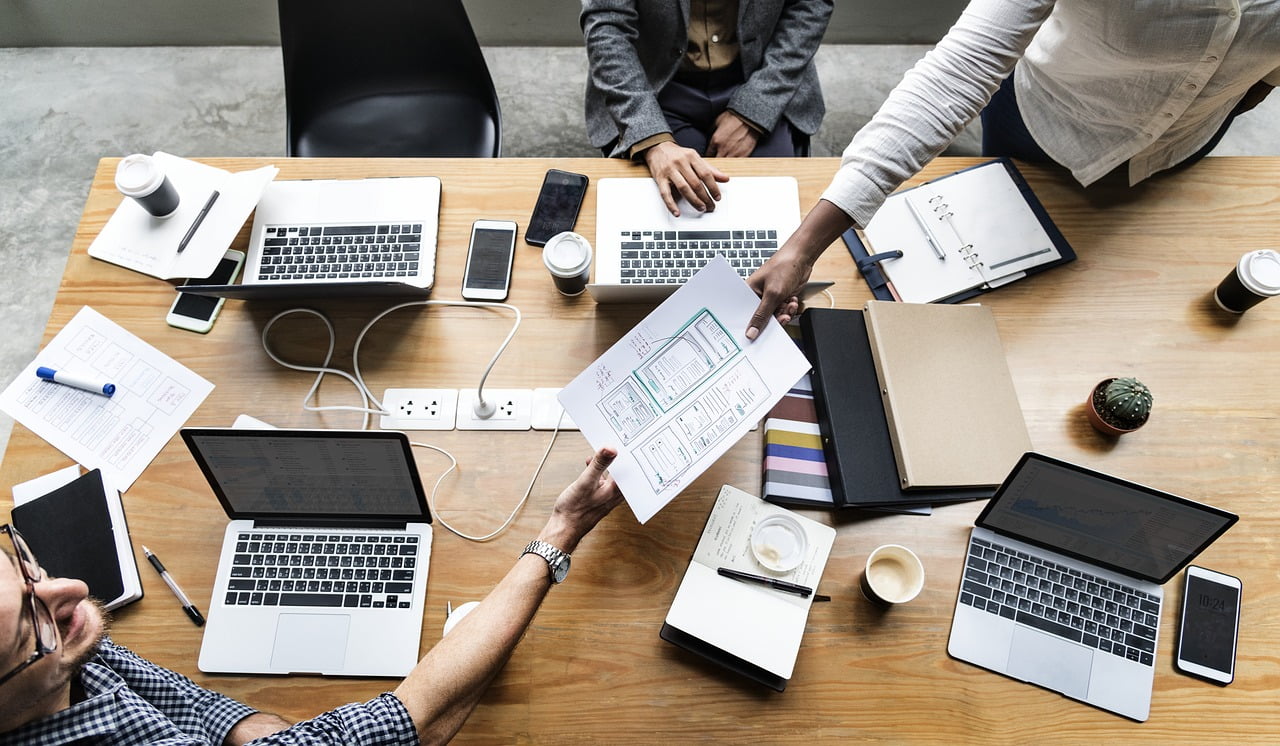
Services
However, there are a few of the steps that we follow when making an estimate:
- 1-2 weeks is generally a good time frame for brainstorming and concept development work
- Market study can add days to the front end of a budget
- It is always good to make a really rough proof of concept model
- 3D CAD development can be done in a few days for something simple. Whereas it would likely take weeks for something more complicated.
- Engineering for final production is usually done as a final step
To illustrate: a large client asking for a product update probably won’t need our services regarding market strategies or intellectual property patenting. It will usually be an iteration of the previous generation. They could also ask us to give them a hand to produce units during the manufacturing process.
On the other hand, a small client with an innovative idea must start from the beginning of the design process. They need to know about their target market, to understand what a realistic retail cost range is. Additionally, they could expect a longer prototyping phase than that of the larger client. This is because their vision of the final product may not be as rigid and could require more iterations.
Innovation
Another important factor to take into account is the road to discovery. When developing a product, there will most likely be unforeseen opportunities for innovation or complications which arise. Sometimes these opportunities can’t be ignored and change the entire scope of the project. These discoveries could be issues with the product that had gone overlooked. Or additional features that would greatly improve the user-experience. Altogether, this means that sometimes the work required will exceed the original quote and add to the budget. For that reason, the budget is always open-ended.
Every client is different. We have had projects last from one week to many years. It all depends on what each client needs for their specific product.
More importantly, SurfaceID offers turnkey product development services. We don’t limit ourselves strictly to industrial design. We can assist you form concept sketching, to manufacture, to mechanical engineering, and more! Don’t hesitate to contact us if you would like to hear more about our services.
Example
Disclaimer: The following numbers are NOT representative of our prices nor are they meant as broad generalizations. They are merely an illustration of how a quota estimate is reached.
Let’s say a big client wants to build a lightweight, weatherproof flashlight. They want to produce 50,000 units and the retail price is projected to be around $25. They contact an industrial design firm and provide them with the internal hardware. For everything else, the firm has total freedom of design. In this case, it really means that the designers will have to find the perfect balance between appeal, ergonomics and durability.
Concept Development
Industrial design studies can take upwards of 80 hours for even a simple electronic device. This includes:
- Product and market research
- Brainstorm and concept direction
- Concept sketching for different form factors
- Detailed design development. This includes human factors, textures and materials
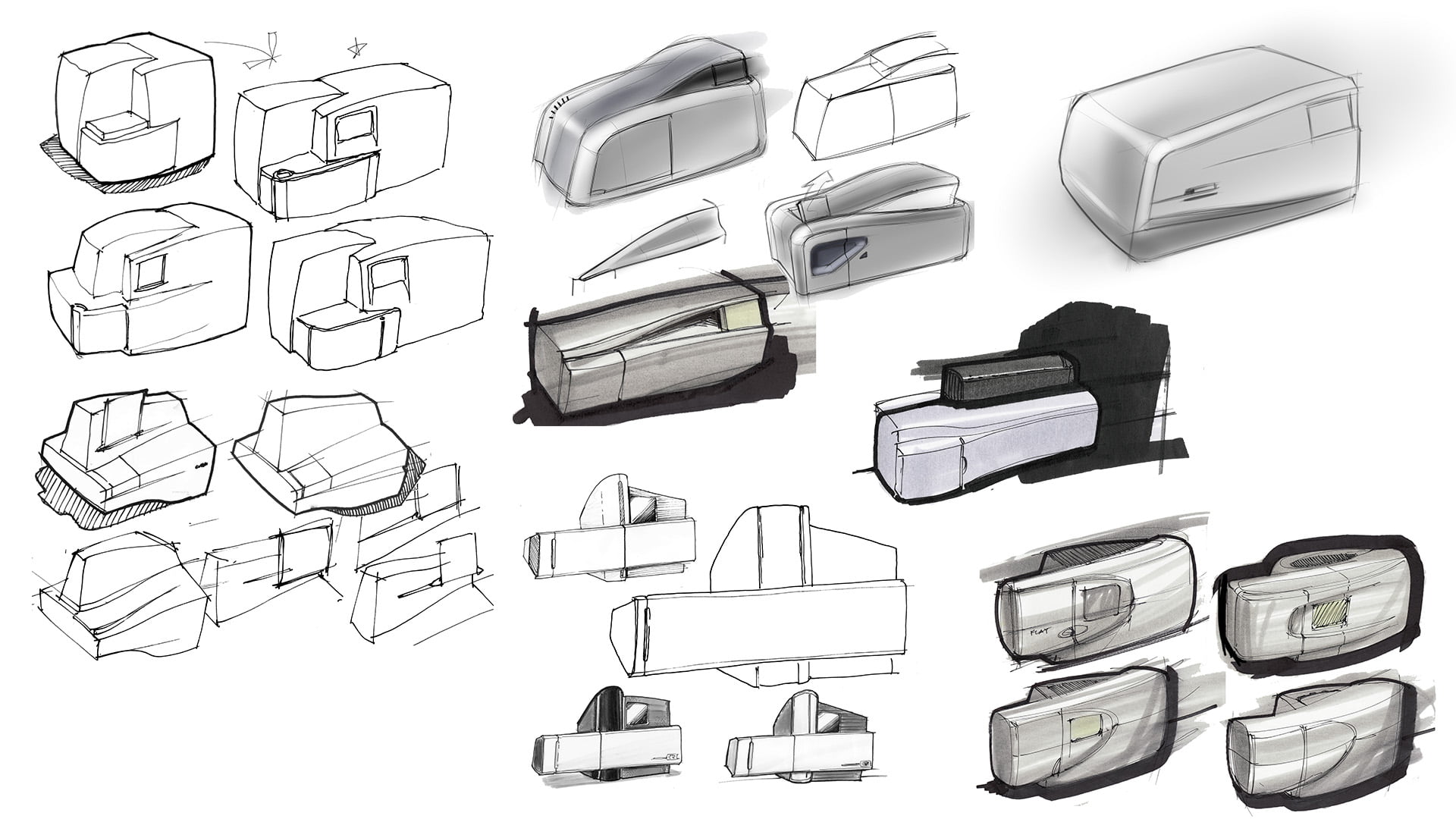
Computer Generated Design (CAD)
Also, clients will most likely require the production of a CAD 3D model which will come at an additional cost. This includes:
- Advanced mechanical and electrical engineering
- Production ready CAD development
- Contact with our manufacturing network
- Building 3D models and physical prototypes
Production and Tooling
Next, the industrial design firm tells the client it would cost about $15,000 to $20,000 to hire them. To put this into perspective:
$20,000 / 50,000 units = $0.4
The cost of industrial design research per unit seems almost negligible now. Yet it is important to invest in ID when developing a product, as it will greatly improve customer experiences and potentially amplify the sales volumes.
Another way to look at the cost of ID is as a percentage the inherit costs of a product. A client who has developed a brand new product would also have to invest in new tooling for manufacture. Their injection mold alone could cost $12,000.
Let’s assume that the determined retail price of each unit would be $23.99 and each unit costs $20 to put on the market. The production cost would encompass everything from manufacturing to packaging, shipping, taxes, etc. For 50,000 units, the total cost would equal $1,000,000.
Overall, the whole project has cost over $1,032,000 to finance. More importantly, less than 2% of that is budgeted for industrial design.
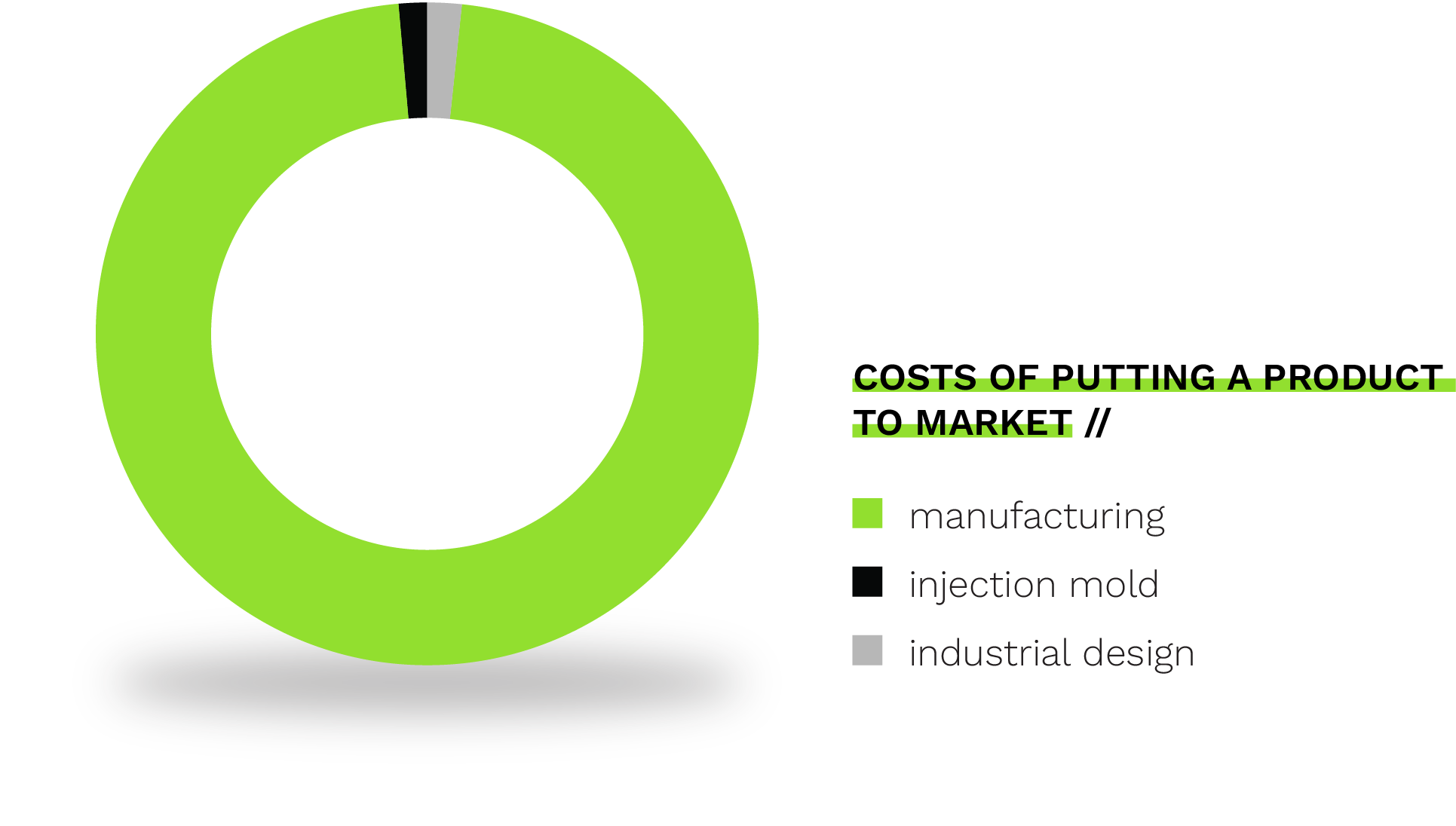
Conclusion
Despite how fundamental industrial design is for a project, its cost is minor compared to the overall expenses. A well designed product will also reduce expenses by optimizing manufacture and materials. Therefore, it is often unwise to try to skimp on industrial design in order to save less than 2% of the budget. Ultimately, your investment will reap the rewards from conception to production.